Beyond Traditional Textiles: How Non-Woven Materials Are Shaping the Future of Industry
Non-woven fabrics are unique textile materials that break away from traditional weaving methods. These innovative fabrics are created by bonding fibres together through chemical, mechanical, heat, or solvent treatments, making them faster and more cost-effective to produce than conventional woven textiles.
Unlike woven or knitted fabrics that require careful yarn preparation and intricate pattern work, non-woven materials can be manufactured directly from fibres. This streamlined process allows manufacturers to create specialised materials for specific uses, from medical supplies to industrial filters.
The versatility of non-woven textiles has revolutionised many industries. These materials can be engineered to be exceptionally strong, remarkably lightweight, or highly absorbent, depending on their intended use. They appear in everyday items like tea bags, disposable nappies, and surgical masks.
On This Page
Key Takeaways
- Non-woven fabrics offer a faster, more economical manufacturing process compared to traditional textiles
- Different bonding methods create unique properties suited for specific applications in medical, industrial, and consumer goods
- These materials contribute to sustainable manufacturing through reduced water usage and energy consumption
Historical Context and Material Development
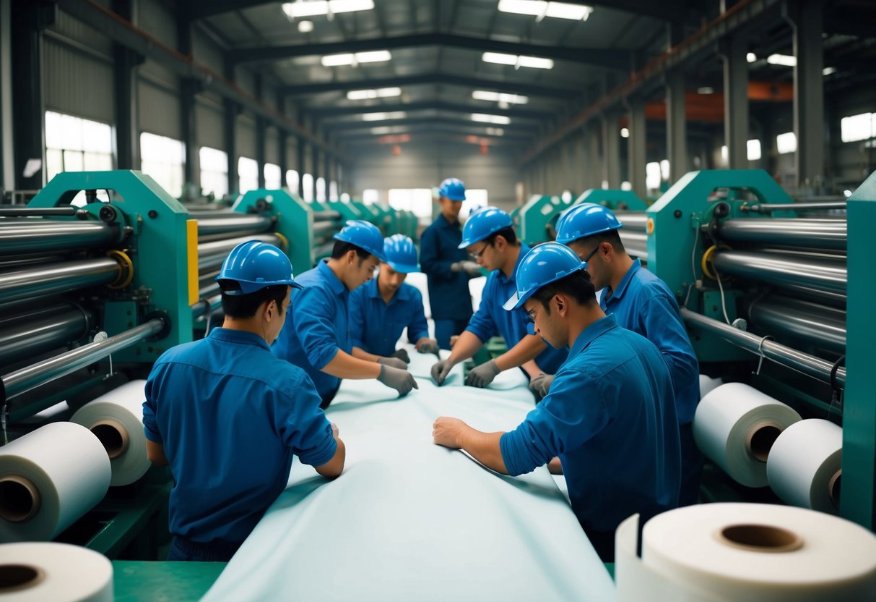
Non-woven fabrics emerged as a revolutionary alternative to traditional textiles, with roots dating back to ancient felt-making techniques. Modern manufacturing processes have transformed these materials into versatile products used across industries.
Evolution from Woven Fabrics to Non-woven Fabrics
Felt stands as one of the oldest non-woven fabrics, created through a process of wetting, compressing, and rubbing wool fibres together. This early technique demonstrated the potential of creating textiles without weaving.
The textile industry took a significant leap in the 1940s when manufacturers began adapting existing equipment to create non-woven materials. The first formal definition of non-woven fabrics emerged in 1962 from the American Society for Testing and Materials.
These materials offered distinct advantages over traditional woven fabrics:
- Faster production times
- Lower manufacturing costs
- Greater flexibility in material properties
Non-woven Fabric Innovations in the Textile Industry
The late 1950s marked a crucial development when paper machines were modified to produce wet non-woven fabrics. This innovation opened new possibilities for material production.
A significant breakthrough came with the spunlace technique. Though patented between 1958 and 1962, large-scale production didn’t begin until the 1980s.
The manufacturing processes expanded to include:
- Mechanical bonding
- Thermal bonding
- Chemical bonding techniques
Modern non-woven fabrics now serve diverse applications, from medical supplies to industrial materials. Their production continues to evolve with new technologies and manufacturing methods.
Types and Properties of Non-woven Fabrics
Non-woven fabrics are engineered materials made from natural or synthetic fibres bonded together through mechanical, thermal, or chemical processes. These versatile materials offer unique characteristics that set them apart from traditional textiles.
Distinct Characteristics of Different Non-woven Materials
Spunlace non-woven fabrics are soft yet strong, making them ideal for medical supplies and baby wipes. They combine durability with excellent liquid absorption.
Synthetic fibres like polyester and polypropylene create robust non-woven materials with high tensile strength. These materials resist tears and maintain their shape under stress.
Stitch-bonded non-wovens use a special knitted loop structure that creates extra strength. This type works well for geotextiles and industrial applications.
Natural fibres like cotton and rayon produce breathable non-wovens that feel soft against the skin. These materials excel in personal care products and medical dressings.
Comparative Analysis of Non-woven Fabrics with Woven and Knit Fabrics
Non-woven fabrics can be produced faster and more economically than traditional textiles. They don’t require the complex yarn-making and weaving processes.
The random fibre orientation in non-wovens creates materials that are:
- More absorbent than woven fabrics
- Better at filtering particles
- Easier to mould into different shapes
Non-wovens typically have lower tear strength compared to woven fabrics. Yet they can be engineered for specific strength requirements by adjusting fibre type and bonding methods.
These materials offer superior insulation properties and air permeability compared to traditional textiles. This makes them excellent for filtration and thermal applications.
Manufacturing Techniques and Processes
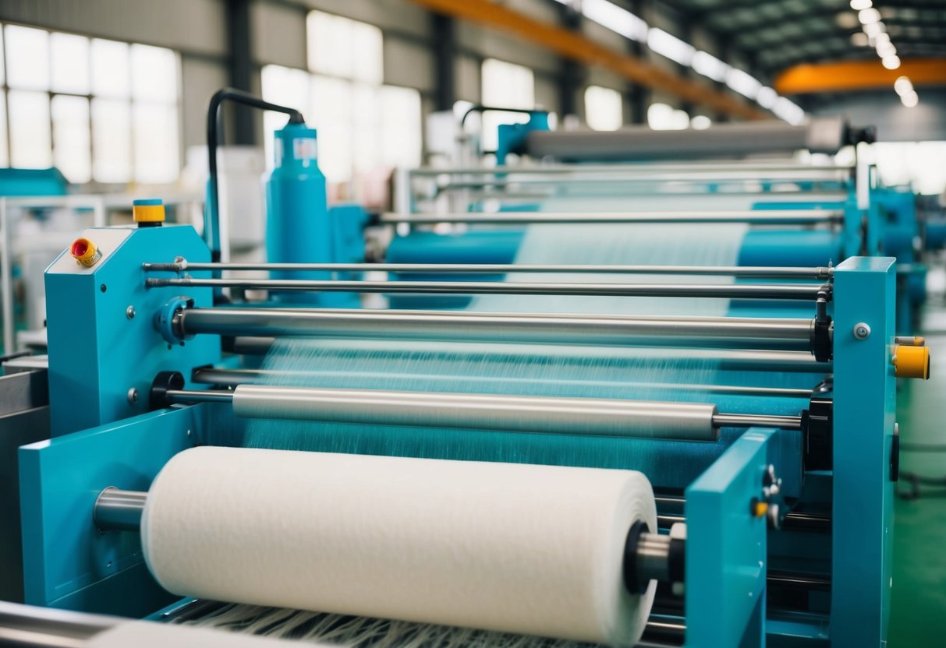
Non-woven fabric manufacturing relies on advanced techniques to transform raw fibres into durable textiles without traditional weaving. The process combines specialised fibre laying methods with various bonding techniques to create materials for diverse applications.
Spunbond and Meltblown Technologies
Spunbond technology creates fabric by extruding molten polymer into continuous filaments. These filaments cool and bond together to form a strong, uniform sheet.
The spunlace process uses high-pressure water jets to entangle fibres, creating a soft, durable material ideal for medical and hygiene products.
Meltblown technology produces ultra-fine fibres by blowing hot air onto melted polymers. This creates extremely fine filaments that form lightweight materials perfect for filtration.
Chemical, Mechanical, and Thermal Bonding Methods
Different bonding techniques secure fibres together to create stable fabrics:
Chemical Bonding
- Spray bonding with adhesives
- Foam binding for soft materials
- Solvent-based treatments
Thermal Methods
- Calendar bonding using heated rollers
- Ultrasonic bonding for synthetic fibres
- Hot air treatment
Mechanical bonding uses needles or water jets to interlock fibres. This method creates strong materials without chemicals or heat.
The choice of bonding method affects the fabric’s strength, flexibility, and intended use. Each technique produces unique properties suited for specific applications.
Functional Attributes and Applications
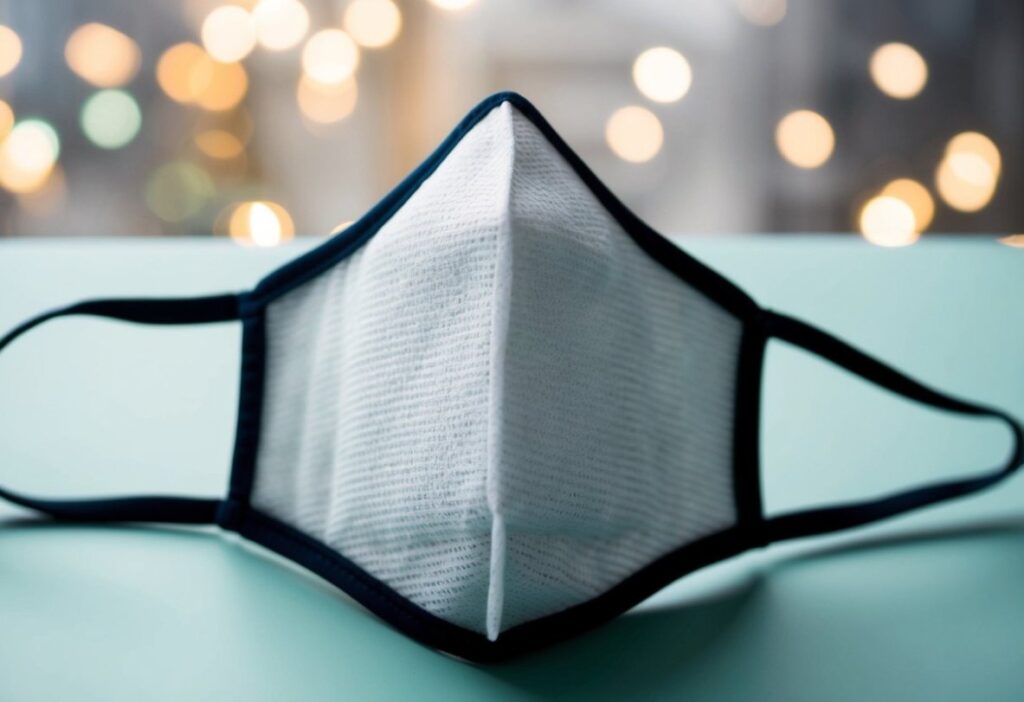
Non-woven fabrics excel in specialised applications due to their unique manufacturing process that creates strong, adaptable materials without weaving or knitting. These versatile textiles offer excellent absorption, filtration, and strength properties.
Use in Hygiene Products and Medical Sector
Medical and hygiene applications rely heavily on non-woven fabrics due to their superior absorption and bacterial barrier properties. These materials form the core components of disposable nappies, feminine hygiene products, and adult incontinence items.
Surgical masks and gowns made from non-woven fabrics provide essential protection in medical settings. The multi-layered structure creates an effective barrier against fluids and microorganisms whilst remaining breathable and comfortable.
The materials offer excellent bacteria filtration efficiency (BFE) ratings, making them ideal for sterile packaging and medical instrument wraps. Their disposable nature helps prevent cross-contamination in healthcare environments.
Industrial and Environmental Applications
Non-woven fabrics serve crucial roles in environmental protection through geotextile applications. These materials stabilise soil, prevent erosion, and facilitate proper drainage in construction projects.
Industrial filtration systems benefit from non-woven materials’ ability to trap particles whilst maintaining airflow. They’re used in:
- Air filtration systems
- Liquid filtration units
- Automotive fuel filters
- Industrial dust collectors
The durability of non-woven fabrics makes them excellent for protective clothing in industrial settings. They resist tears, chemicals, and extreme temperatures whilst remaining lightweight and comfortable.
Product Examples and Consumer Goods
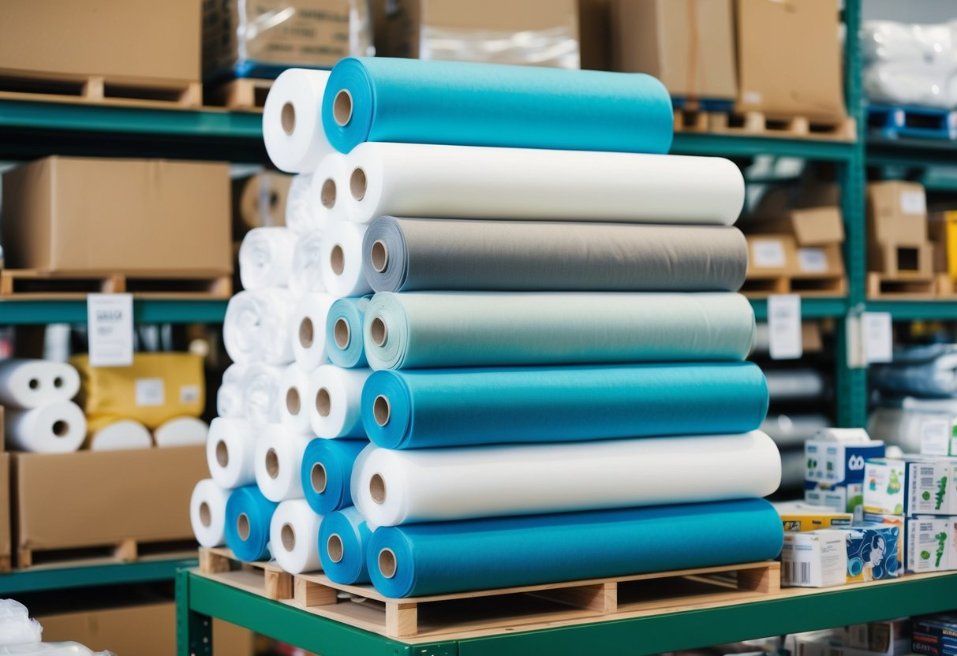
Nonwoven fabrics serve as essential materials in many everyday items. Their unique bonding process creates versatile materials that offer superior absorption, strength and cost-effectiveness.
Wipes, Nappies, and Feminine Hygiene Products
Dryer sheets and cleaning wipes demonstrate the durability of nonwoven materials in high-temperature and wet conditions. These products maintain their structure while releasing cleaning agents or fabric softeners.
Baby nappies rely on nonwoven fabrics for their absorbent core and soft outer layers. The materials trap moisture away from the skin while remaining breathable and comfortable.
Feminine hygiene products utilise multiple layers of nonwoven fabrics. The top layer provides comfort, while inner layers offer superior fluid absorption and distribution.
Market Presence in Furniture Upholstery and Garment Interfacing
Furniture manufacturers use nonwoven materials as backing and padding in upholstered pieces. These materials provide structure and support while reducing manufacturing costs.
Garment interfacing made from nonwoven textiles adds shape and stability to collars, cuffs, and waistbands. The material bonds well with fabric and maintains its structure through repeated washing.
Common applications include:
- Sofa and chair cushioning
- Decorative panel backing
- Collar stiffeners
- Waistband supports
Physical and Mechanical Properties
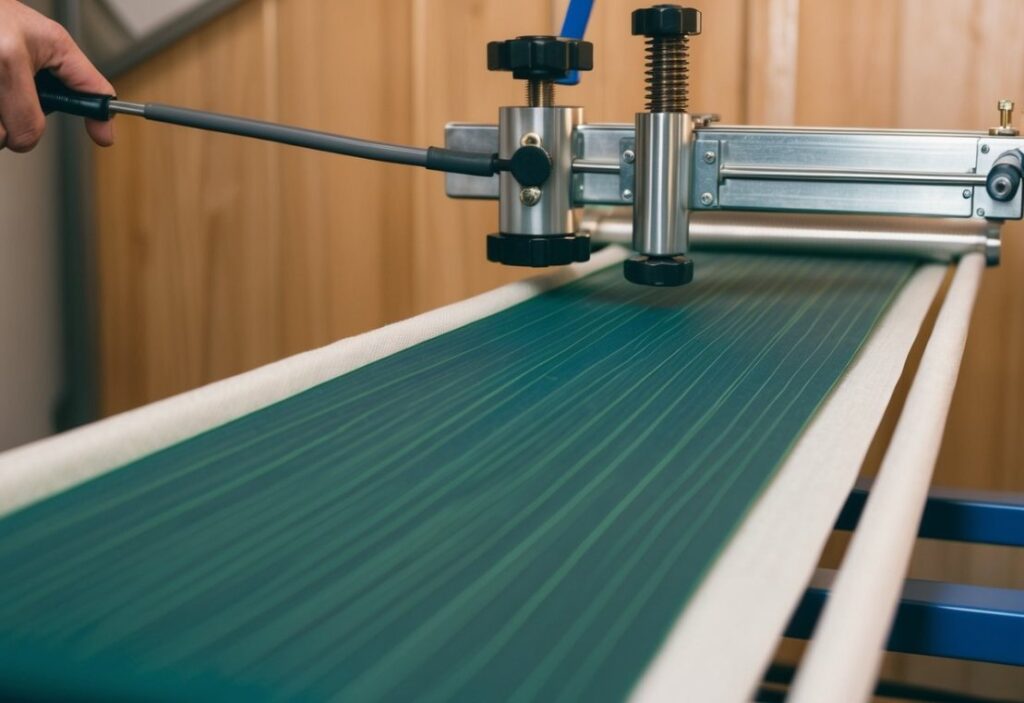
Non-woven fabrics possess distinct physical and mechanical characteristics that stem from their unique fibre arrangement and bonding methods. These properties determine their performance in various applications.
Strength, Stretch, and Absorbency Factors
Non-woven materials demonstrate varying levels of tensile strength based on their manufacturing process and fibre composition. The random arrangement of fibres creates a structure that can withstand different types of stress.
Their stretch capabilities depend on:
- Fibre orientation
- Bonding technique
- Material thickness
- Fibre type
Water absorption varies significantly among different non-woven types. Some fabrics show excellent absorbency for filtration and hygiene products, whilst others feature water-repellent properties for protective gear.
Porosity, Resilience, and Softness Characteristics
The structural parameters of non-woven fabrics directly influence their porosity levels. The spaces between fibres create pathways for air and moisture movement.
Key softness factors include:
- Fibre fineness
- Surface texture
- Bonding density
- Manufacturing method
Resilience characteristics depend on the fibre type and bonding process. Materials can range from highly elastic to rigid, with some bouncing back to their original shape after compression.
Physical testing shows that non-woven fabrics can maintain their properties even after repeated use, making them suitable for both disposable and durable applications.
Sustainability and Environmental Impact
Non-woven fabrics present complex environmental trade-offs, with both advantages in resource efficiency and challenges around disposal and recyclability. Their production methods can use less water and energy compared to traditional textiles, yet their often synthetic composition raises important sustainability questions.
Eco-friendly Alternatives and Life Cycle Analysis
Sustainable non-woven materials are emerging in the fashion and textile industries as alternatives to conventional options. These materials reduce environmental impact through innovative production processes.
Several manufacturers now use recycled polyester and natural fibres to create more environmentally friendly products. These alternatives consume up to 91% less water than traditional manufacturing methods.
Non-woven fabrics can be more resource-efficient during production and use. They often require less energy for maintenance since many types don’t need laundering.
Waste Management and Recycling Challenges
Single-use applications of non-woven fabrics create significant waste management issues. These materials frequently end up in landfills after just one use.
The shorter lifespan of non-woven materials compared to woven fabrics means more frequent replacement. This creates additional waste and increases long-term costs.
Many synthetic non-woven materials release microplastics during breakdown. These particles can harm marine ecosystems and enter the food chain.
Current recycling systems struggle to process mixed-material non-woven fabrics effectively. This limitation makes proper disposal challenging and often leads to increased environmental impact.
Frequently Asked Questions
Non-woven fabrics serve essential roles across industries like healthcare, automotive and filtration through their unique manufacturing methods and properties. These versatile materials offer specific advantages in durability, cost-effectiveness and customisation potential.
What are some common uses for non-woven fabrics?
Non-woven materials are widely used in medical gowns, face masks and surgical drapes due to their protective barrier properties.
They also play crucial roles in automotive interiors, furniture upholstery and geotextiles for construction projects.
Filtration systems rely heavily on non-woven fabrics for air, water and oil filters due to their customisable pore sizes and high surface area.
How is non-woven fabric produced and what raw materials are used?
Non-woven fabric production involves bonding fibres together through mechanical, thermal or chemical processes rather than weaving.
Common raw materials include synthetic fibres like polypropylene and polyester, as well as natural fibres such as cotton and wood pulp.
The manufacturing process typically involves web formation, bonding and finishing treatments to achieve desired properties.
Can non-woven fabrics be recycled, and if so, how?
Single-material non-woven products made from synthetic fibres can be mechanically recycled into new materials.
Some manufacturers now offer recyclable non-woven options made from biodegradable materials or recycled content.
The recycling process involves shredding, melting and reforming the fibres into new non-woven products.
In what ways do non-woven fabrics differ from woven fabrics?
Non-woven fabrics are created by directly bonding fibres together rather than interlacing yarns.
They typically offer greater flexibility in thickness, porosity and strength compared to woven materials.
Non-woven production is generally faster and more cost-effective than traditional weaving processes.
What are the main characteristics and advantages of non-woven fabrics?
Non-woven fabrics provide excellent absorbency, liquid repellency and bacterial filtration depending on their construction.
These materials offer strong durability whilst remaining lightweight and often more economical than traditional textiles.
Their adaptable manufacturing process allows for customised properties like flame resistance or antimicrobial treatments.
How can one identify high-quality non-woven fabric suppliers?
Look for suppliers with proper quality certifications and testing capabilities for their materials.
Request material samples and specifications to verify performance characteristics meet required standards.
Evaluate the supplier’s manufacturing consistency and their ability to maintain stable product quality across batches.
Related Posts: