Journey from raw fiber to finished textile through the intricate processes that bring our everyday materials to life
Fabrics are essential materials that surround us daily in our clothes, home furnishings, and countless other items. The process of creating fabric involves transforming natural and synthetic fibres into cloth through complex manufacturing techniques like spinning, weaving, and knitting.
The journey from raw material to finished fabric starts with either natural fibres like cotton and wool or synthetic materials like polyester. These fibres are spun into threads which are then woven or knitted together on specialised machines to create different types of textile materials.
Modern fabric production often combines different materials to create blended fabrics with enhanced properties. For example, polycotton mixes cotton and polyester to create a fabric that is both breathable and crease-resistant.
On This Page
Key Takeaways
- Natural and synthetic fibres are transformed into yarn through spinning processes
- Fabric creation relies on weaving or knitting techniques to interlock threads
- Modern textile production combines different materials to enhance fabric properties
The Basics of Fabric Construction
Fabrics start as raw fibres that are spun into yarn and then constructed into textiles through various techniques. The properties of the final fabric depend on both the materials used and the construction methods.
Types of Fibres
Natural fibres come from plants and animals. Cotton fibres grow around cotton plant seeds and create soft, breathable fabrics. Wool comes from sheep and other animals, providing warmth and natural water resistance. Silk, produced by silkworms, creates smooth, luxurious textiles.
Synthetic fibres are made in laboratories and factories. Polyester, nylon, and acrylic are common examples. These fibres offer benefits like:
- Higher durability
- Easier care
- Lower cost
- More consistent quality
Yarn Formation
Yarn creation involves twisting fibres together to form long, continuous strands. The process includes:
Cleaning: Removing dirt and debris from raw fibres
Carding: Aligning and smoothing fibres into a uniform direction
Drawing: Stretching the fibres to create an even thickness
Spinning: Twisting the fibres together to create yarn
Fabric Weaves
Weaving creates fabric by interlacing yarns at right angles. The vertical yarns are called the warp, while horizontal yarns are the weft.
Basic weave patterns include:
- Plain weave: Simple over-under pattern
- Twill weave: Creates diagonal lines
- Satin weave: Produces a smooth, glossy surface
The weave pattern affects the fabric’s strength, appearance, and drape.
From Fibre to Fabric
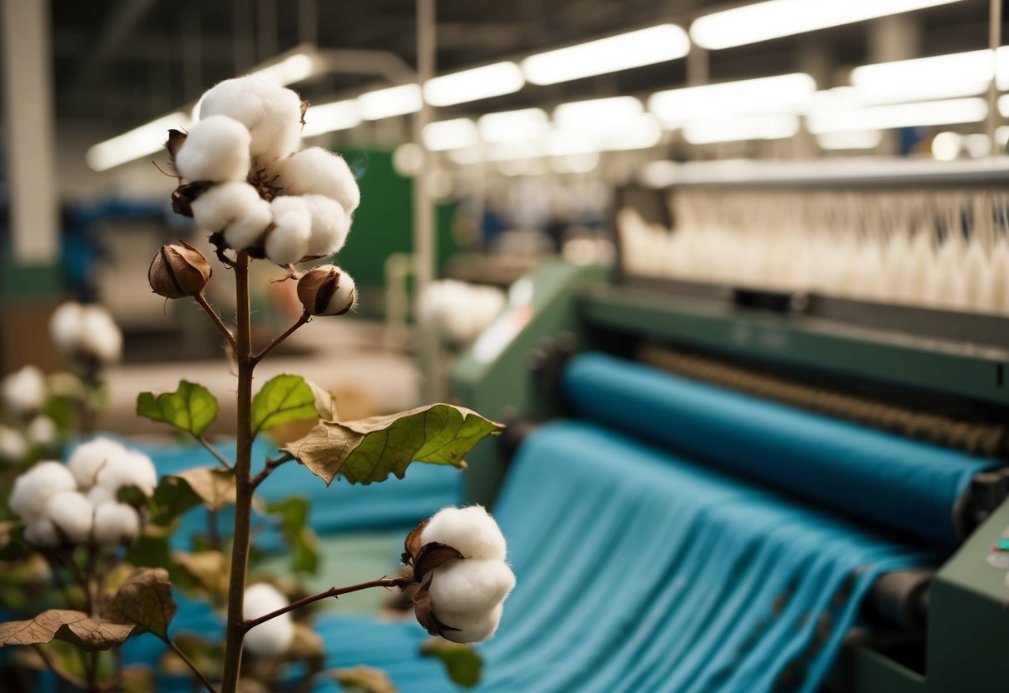
The creation of fabric involves several precise steps that transform raw fibres into usable material. The process starts with cleaning the raw material, moves through careful preparation steps, and ends with spinning the fibres into yarn.
Ginning and Cleaning
Raw fibres must be cleaned and separated before they can become fabric. Natural fibres like cotton arrive with seeds and debris mixed in with the useful parts.
The ginning machine removes seeds from cotton bolls while preserving the cotton fibres. This crucial step prevents damage to the delicate strands.
For wool fibres, the cleaning process involves washing with special detergents to remove natural oils, dirt, and plant matter. This washing makes the wool ready for the next steps.
Carding and Combing
Carding arranges fibres into a loose rope-like form called a sliver. The process uses rotating cylinders covered in tiny wire hooks.
The sliver passes through combing machines that remove short fibres and align the remaining ones. This creates stronger, more uniform yarn.
Key benefits of proper carding and combing:
- Removes remaining debris
- Straightens and parallels fibres
- Creates consistent fibre density
- Improves final yarn quality
Spinning
Spinning transforms the prepared fibres into yarn through twisting. The amount of twist affects the yarn’s strength and texture.
Modern spinning machines can produce different yarn types:
- Single yarns
- Plied yarns (multiple yarns twisted together)
- Textured yarns
The spinning frame draws out the fibres and adds twist in one continuous motion. This creates yarn that’s ready for weaving or knitting into fabric.
Weaving and Knitting Techniques
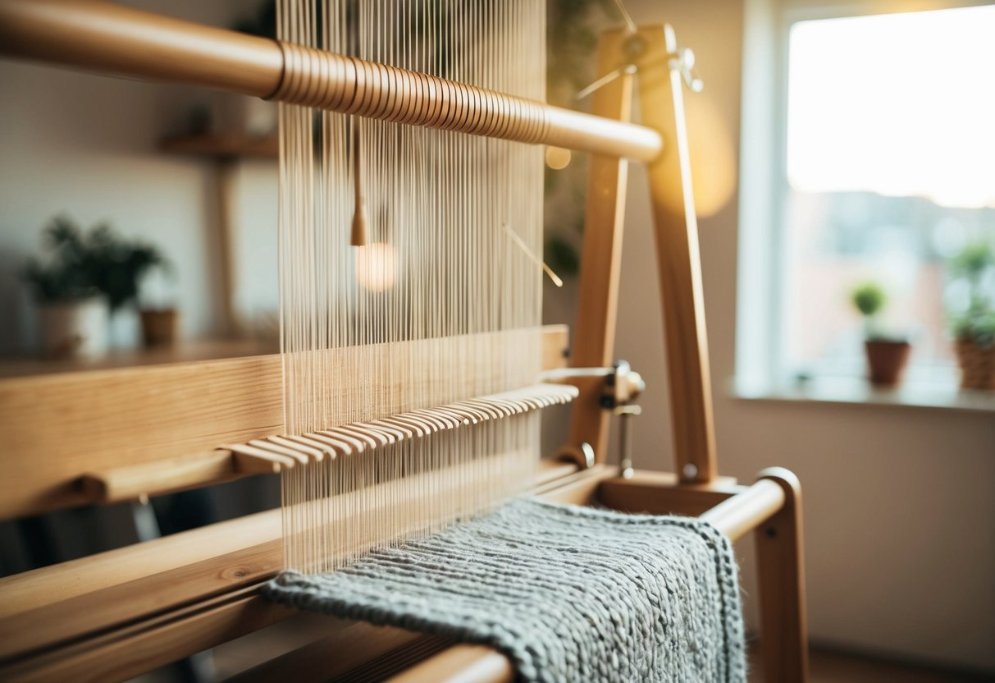
Fabrics come to life through distinct manufacturing methods that create unique textures and properties. Woven and knitted fabrics form the backbone of textile production, each offering specific advantages for different uses.
Weaving Patterns
Weaving involves interlacing vertical and horizontal yarns called warp and weft. The warp yarns run lengthwise, whilst the weft yarns cross from side to side.
Plain weave is the most basic pattern. It creates a strong, balanced fabric by passing weft threads alternately over and under each warp thread.
Satin weave produces a smooth, glossy surface. The technique allows longer thread floats by skipping several intersections before interlacing.
Woven fabrics tend to be:
- More stable and durable
- Less stretchy
- Excellent for structured garments
- Resistant to snags
Knitting Styles
Knitted fabrics form through interlocking loops of yarn. The construction is looser than weaving, creating natural stretch and flexibility.
Weft knitting uses a single yarn that forms horizontal rows of loops. This common technique creates t-shirts and jumpers.
Warp knitting requires multiple yarns working vertically. It produces stable fabrics used in:
- Swimwear
- Athletic wear
- Lingerie
- Technical textiles
Non-Woven Fabrics
Non-woven fabrics skip the yarn stage entirely. Fibres bond together through mechanical, thermal, or chemical processes.
These fabrics offer unique benefits:
- Quick and cost-effective production
- No yarn preparation needed
- Excellent for disposable items
- Strong filtering capabilities
Common non-woven products include medical masks, disposable wipes, and interfacing materials used in garment construction.
Types and Treatments of Fabrics
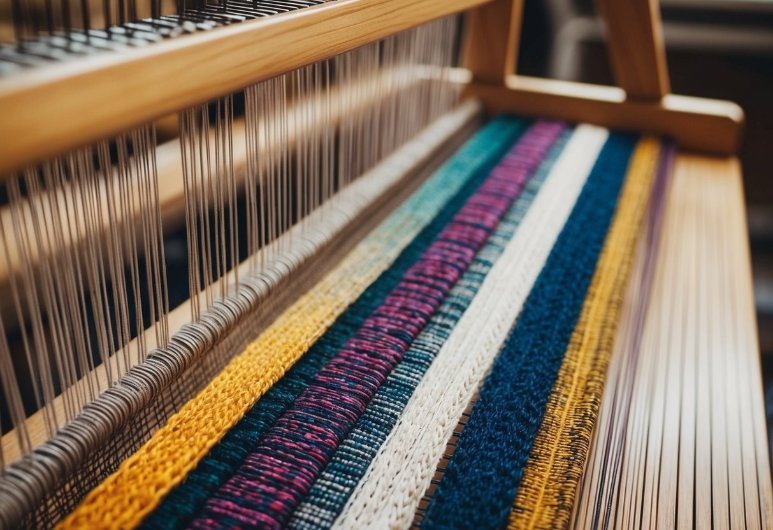
Fabrics come in many forms, from pure natural fibres to synthetic materials and carefully engineered blends. Their properties can be enhanced through specialised chemical and physical treatments.
Natural vs Synthetic Fabrics
Natural fibres like cotton, wool, and silk come from plants and animals. Cotton contains cellulose fibres that make it breathable and comfortable against the skin. Wool offers excellent insulation and natural water resistance. Silk provides a smooth, luxurious feel with good temperature regulation.
Synthetic fabrics are made through chemical processes. Nylon offers incredible strength and durability. Polyester resists wrinkles and maintains its shape well. Rayon, made from processed wood pulp, combines natural and synthetic properties.
Acrylic mimics wool’s warmth while being lighter and less expensive. Elastane adds stretch and flexibility to garments.
Fabric Blends
Different fibre types can be combined to create fabrics with enhanced properties. Cotton-polyester blends offer durability while maintaining comfort. Wool-acrylic combinations provide warmth at a lower cost.
Popular blends include:
- Cotton/elastane for stretch in denim
- Wool/polyester for wrinkle-resistant suits
- Nylon/spandex for athletic wear
These combinations help overcome the limitations of single-fibre fabrics.
Fabric Finishing Processes
Chemical treatments and finishing processes improve fabric properties. Anti-wrinkle treatments help garments maintain their shape. Water-resistant coatings protect against rain and stains.
Common finishing treatments include:
- Mercerisation for increased strength and lustre in cotton
- Flame retardant applications for safety
- Softening agents for improved texture
These processes transform basic textiles into high-performance materials with specific properties for different uses.
Fabric Structure and Design
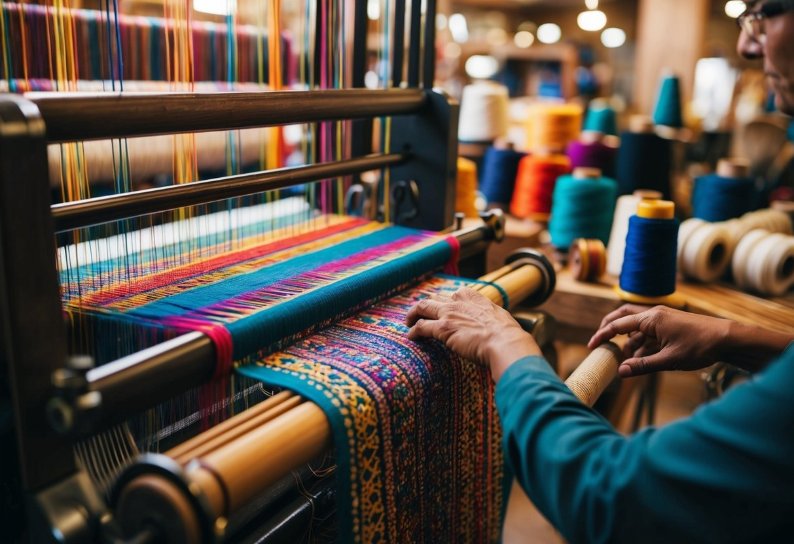
Fabric structure refers to how yarns are interlaced to create textiles. The way these yarns connect determines the fabric’s strength, appearance, and performance.
Understanding Warp and Weft
Woven fabrics are created by interlacing two sets of yarn at right angles. The warp yarns run lengthwise, whilst the weft yarns run across the width.
The most basic weave is plain weave, where weft yarns go over and under each warp yarn alternately. This creates a strong, stable fabric.
Twill weave creates diagonal lines by passing weft yarns over two or more warp yarns. Denim is a popular example of twill weave.
Satin weave has longer yarn floats, creating a smooth, glossy surface. These fabrics often have a luxurious appearance but can be less durable.
Fabric Textures and Qualities
Different weave patterns create unique textures and properties. Non-woven fabrics are made by bonding fibres together rather than weaving.
Pile fabrics like velvet have extra yarns that stand up from the base fabric. This creates a soft, deep texture.
The tightness of the weave affects:
- Fabric durability
- Drape
- Warmth
- Water resistance
Decorative elements can be added through:
- Embroidery
- Printing
- Special weave patterns
- Textural variations
Fabric in Fashion and Apparel
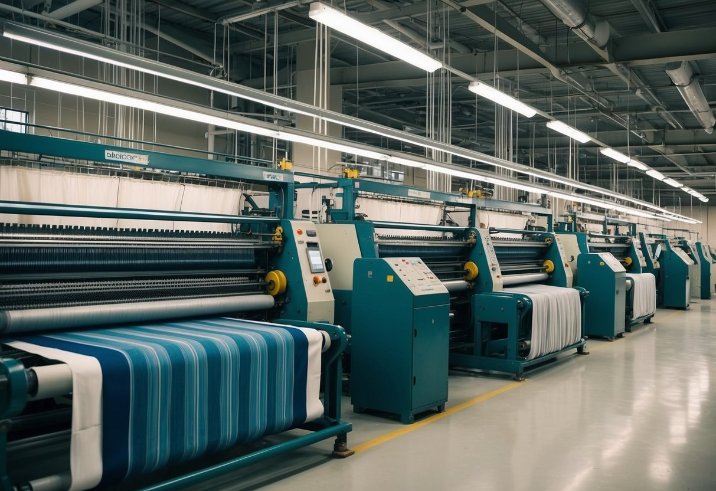
Fashion designers select specific fabrics based on their properties and intended use in garments. The choice of fabric directly impacts how a piece of clothing looks, feels, and functions.
Dresses and Formalwear
Silk, satin, and velvet remain popular choices for elegant dresses and formal attire. These fabrics create fluid movement and catch light beautifully.
Velvet adds a luxurious touch to evening gowns and formal jackets. Its pile construction creates depth and warmth, making it ideal for winter formal events.
Common Formal Fabrics:
- Silk chiffon for flowing dresses
- Taffeta for structured gowns
- Crepe for draped designs
- Lace for detailed overlays
Casual and Sportswear
Different types of fabric serve specific purposes in casual wear. Cotton dominates the t-shirt market due to its breathability and comfort.
Denim, used in jeans and jackets, offers durability and versatility. Modern stretch denim includes elastane for improved movement.
Sportswear Innovations:
- Moisture-wicking polyester for tops
- Compression fabrics for tights
- Breathable mesh for ventilation
- Four-way stretch materials for flexibility
Specialty Fabrics
Technical fabrics combine multiple properties to enhance performance. These materials often feature special coatings or treatments.
Smart textiles incorporate technology for temperature regulation in jumpers and outerwear. Some fabrics offer UV protection for outdoor activities.
Advanced Features:
- Water-resistant coatings
- Anti-bacterial treatments
- Thermal regulation
- Stain-resistant finishes
Care and Maintenance of Fabrics
Proper fabric care starts with sorting clothes by colour, type, and level of dirt. This simple step prevents colour bleeding and fabric damage.
Natural fibres like cotton need different care than synthetic materials like polypropylene. Cotton can handle hot water, while synthetics need cooler temperatures to prevent damage.
Regular washing and cleaning help fabrics last longer. Check garment labels before washing to follow the correct instructions for each type of material.
Key cleaning steps:
- Remove stains promptly
- Sort clothes by colour and fabric type
- Use appropriate water temperature
- Choose suitable washing methods
- Dry items according to care labels
Delicate fabrics like silk and wool need gentle hand washing. These materials can shrink or lose shape in washing machines.
Synthetic fibres are typically easier to care for. They resist wrinkles and dry quickly, but high heat can damage them permanently.
Regular maintenance includes proper storage in clean, dry spaces. Hanging heavy garments helps them keep their shape, while folding delicate items prevents stretching.
Innovations in Fabric Production
Modern fabric production combines cutting-edge technology with sustainable materials to create textiles that are both high-performing and environmentally responsible. New manufacturing methods and eco-friendly fibres are transforming how fabrics are made.
Technological Advancements
Digital technology in fabric production has revolutionised manufacturing processes. Smart textiles now incorporate sensors and electronic components to create fabrics with enhanced functionality.
3D weaving techniques produce stronger and lighter materials than traditional methods. These fabrics offer improved flexibility and durability for specialised applications.
Nanotech innovations allow for the creation of fabrics with special properties. These include water-resistant coatings, antimicrobial treatments, and temperature-regulating features.
Eco-Friendly Materials
Alternative fibres like bamboo and jute are gaining popularity. These materials require less water and fewer chemicals to produce than traditional cotton.
Manufacturers now create viscose using closed-loop systems that reduce environmental impact. This process reuses chemicals and minimises waste water.
Recycled materials are transforming fabric production. Used cotton and polyester are being transformed into new textiles, reducing landfill waste and conserving resources.
Natural dyes and low-impact finishing processes help reduce the chemical footprint of fabric manufacturing. These methods preserve water quality and protect ecosystem health.
Frequently Asked Questions
Creating fabric involves complex processes that have evolved from ancient hand-weaving to modern manufacturing. Different materials and techniques produce unique textiles for various purposes.
What is the step-by-step process of fabric production?
Modern fabric production starts with raw fibres that are cleaned and spun into threads. These threads get woven or knitted together to form the basic fabric structure.
The fabric then undergoes treatments like dyeing, printing, and finishing to add colour and enhance properties. Specialised processes create unique textures, like the extra warp threads used to make velvet’s plush surface.
How were textiles produced in ancient civilisations?
The earliest fabric remains date back to 6,500 BC in Anatolia, near modern-day Turkey. These ancient textiles included woven rugs and wool fragments.
Ancient civilisations used primitive looms and hand-spinning techniques to create fabrics from natural materials like linen, wool, and flax.
What is the method by which cotton is turned into fabric?
Raw cotton fibres are cleaned to remove seeds and debris. The clean fibres are then carded to align them in the same direction.
The aligned fibres are spun into yarn using spinning machines. The yarn is then woven into fabric by interlacing vertical warp threads with horizontal weft threads.
Can you explain the origin of fabric materials?
Fabrics come from two main sources: natural and synthetic. Natural fibres include cotton from seed pods, wool from animals, and hemp from plants.
Synthetic fabrics are manufactured from chemical compounds to create materials like nylon and acrylic.
What are the primary techniques for fabric manufacturing?
The main manufacturing methods are weaving, knitting, felting, braiding, and bonding. Weaving creates strong, stable fabrics by crossing threads at right angles.
Knitting forms fabric by interlocking loops of yarn. Felting compresses loose fibres together without spinning or weaving.
Could you outline the stages involved in creating clothes from fabrics?
Pattern making translates design ideas into paper templates. These patterns guide the cutting of fabric pieces to the correct shapes and sizes.
The cut pieces are sewn together to form garments. Additional elements like buttons, zips, and trims are attached during the final assembly.